Iwata Asks: Wii U GamePad
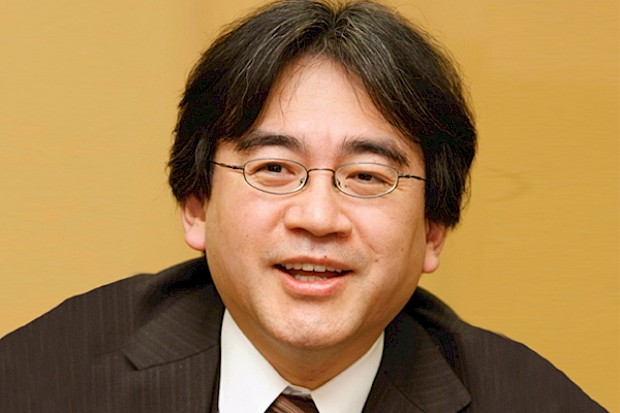
Posted 17 Oct 2012 at 11:39 by Joshua Phillips
The latest Iwata asks (which you can read here in full) focused on the GamePad itself. Read on to find out about the design process, the distance at which you can play and how they managed to create a device with next to no delay.
GamePad distance:
Whilst you can't take the GamePad out in the garden, you can take it into the next room and possibly even further depending on the design of your house. This is according to Toru Yamashita, who worked on the firmware that runs on the Wii U GamePad and the software responsible for connecting it to the Wii U console.
Iwata warned that connectivity depends on your own home though.
"When asked "Can I use it in my bedroom?" we can say that it would work within the same space when there is nothing in the way, but basically it depends on how your house is constructed, so we have to ask that you test it in your own home."
The Design Process
Considering the large screen and face buttons, Nintendo were eager to ensure that the Wii U GamePad was still comfortable to hold even during long play sessions. To ensure this, Nintendo's developers make models of the controllers by hand using clay along with 3D printers.
Masato Ibuki explained the process further, as he worked on the industrial design of the Wii U GamePad.
"This time, instead of using the designs as it had come out of the 3D printer, we actually recieved approval for design with something that all the team members including myself whittled by hand to make fine adjustments to the 3D printed objects in the company workshop.
We carved what came out of the 3D printer by hand and then sanded it. Most of the controller designs approved in the past were fine-tuned by hand. By doing things by hand, each trial and error processes can be done much, much faster, so when the design is in the fine-tuning stage you absolutely need to make modifications by hand."
So it's not just a case of using 3D printers, a lot of hands-on work is also required to fine tune controllers to perfection.
"Besides using a 3D printer, design considerations are done using various techniques. You'll need to not only be able to carve but add and mould, and depending on the situation we use clay to shape objects. When presenting a design for review we recreate it using a 3D printer to make a clean version, and then fine-tuning and detailing that model by hand."
So a lot of hard work had already gone into the design of the Wii U GamePad, but it didn't end there. As some of you may remember, at E3 2011 the GamePad looked a lot more like a tablet, with a flat back. It seems that Miyamoto and Iwata weren't too keen on this design though.
The Design Process: Fine Tuning
When the GamePad returned at E3 2012, it had a new look with grips on the back and clickable analogue sticks. This was thanks to Miyamoto and Iwata.
Iwata stated that the new version of the controller is much more comfortable.
"Both Miyamoto-san and myself wanted the change to happen. It's true that if you held the earlier incarnation of the Wii U GamePad for very long, there were times where your fingers could get tired. That really changed, though."
But just how did they manage to make the controller that much easier to hold? Ibuki describes what changed in the later stages.
"The grips we affixed to the improved version actually weren't finalised until the very end. At first, we looked at a more flat, square shaped pad to a version with gradual grips and considered various options.
It needed to be a design where you wouldn't easily get tired, and we looked into what was the best design that would be the most comfortable for both big and small hands. Ultimately, the design that everyone in the design group agreed was the easiest to use, was the final form with the grips."
So it was back to the workshop for Ibuki and his team, to once again adjust the remote with a mixture of techniques.
Unlike the GameCube, the Wii did not have a handle, Iwata made one out of clay in his own time.
Losing Weight
We're not talking about the developers and designers here, though they no doubt lost weight in the stress of coming up with such a magical device. Instead we are talking about the Wii U controller and the ways in which the team went about making a light-weight device, because despite its appearance, the Wii U GamePad is actually lighter than you think.
According to Ibuki, in order to keep the Wii U GamePad a respectable weight, they used a material called Chassis Resin.
"Making it lighter was important. The engineering group took the lead in making it lighter. With Wii U GamePad we put in a lot of effort in reducing its weight. There is a part called a chassis to protect the screen, and at first, we were planning on using materials like aluminum and magnesium. But ultimately we decided against those and used what's called resin chassis to further reduce its weight. In that way, we chipped awat one or two grams here and there."
Latency Issues
Finally, Nintendo explained how they avoided latency issues. Well, we say "explained" but unless you are 'into' that sort of thing, the best explanation would be to say "we achieved this by magic".
"We thought of a way to take one image and break it down into pieces of smaller images. We thought that maybe we could reduce the amount of delay in sending one screen if we dealt in those smaller images from output from the Wii U console GPU on through compression, wireless transfer, and display on the LCD monitor.
The Wii U can rapidly compress data and when it is a 'packet-size', it sends it to the Wii U GamePad.
So that's the 'shorter' version of Iwata asks with all of the important information plucked out. For the full interview, click here.